Our service for you.
For our products we offer you a service day and night.
In addition to quality inspections, maintenance or repairs, you can also rent and test our test sieve machines. With us, you get the all-round package and everything from a single source.
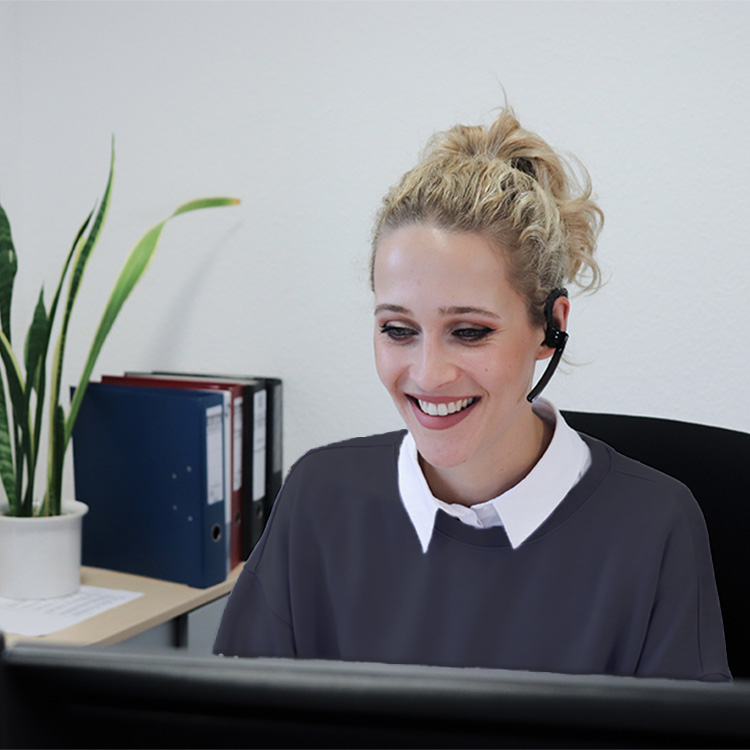
We are at your disposal. Everywhere.
You would like to have your test sieve machine calibrated? Or do you need an appointment for on-site recertification of your test sieves? You would perhaps like to train your employees face-to-face or online on how to optimally implement sieve analysis?
Our competent team of consultants and your personal points of contact are always at your service — by phone, email or on site.
Internationally, our worldwide NEXOPART sales and service network is at your disposal. Those who want to be flexible can also order their laboratory supplies around the clock online through our webshop.
Take a look at what service means at NEXOPART
Download for service offer
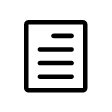
Data sheet
Find out more about the NEXOPART service offer for particle analysis and dynamic image analysis measuring devices.
Maintenance and repairs. At your site. At our site.
Your goal is to avoid unnecessary costs and maintain the productivity of your test sieve machines and instruments. However, external influences or abrasive sieving samples could impair proper operation of your test sieve machines. This is where NEXOPART comes to the rescue: with fast repair services and the right maintenance solutions. Our service experts analyze options for optimizing your sieving machine and possible upcoming repair work at your site or at our site. If repairs are necessary, they will be carried out on site at our factory in Oelde or Gersthofen. If required, please contact us and talk directly to our service experts.
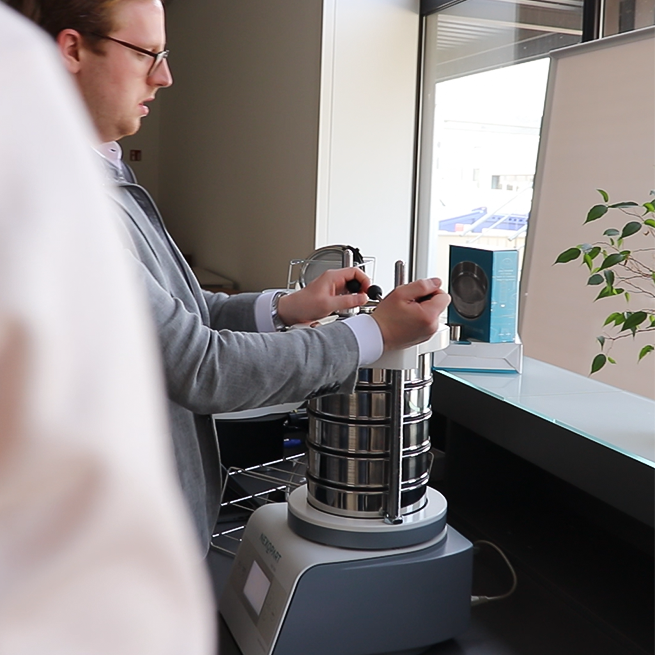
Important note:
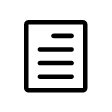
Dear customers, please keep in mind that the declaration of no objection, which you can download here, must be filled out and sent to NEXOPART in case of a reparation at the factory. Please understand that deliveries without a declaration of no objection cannot be processed.
Download now-
Delivery in original packaging on a Euro pallet.
Please note: Damaged packages will not be accepted. - Declaration of no objection and cleaned device.
- Return bill with work instructions: Precise details of the necessary measures.
For repairs: Precise description of the defect/problem.
- Enclose accessories:
- PSU with cable.
- In case of pressure problems, suction cup and CBX box/power contactor.
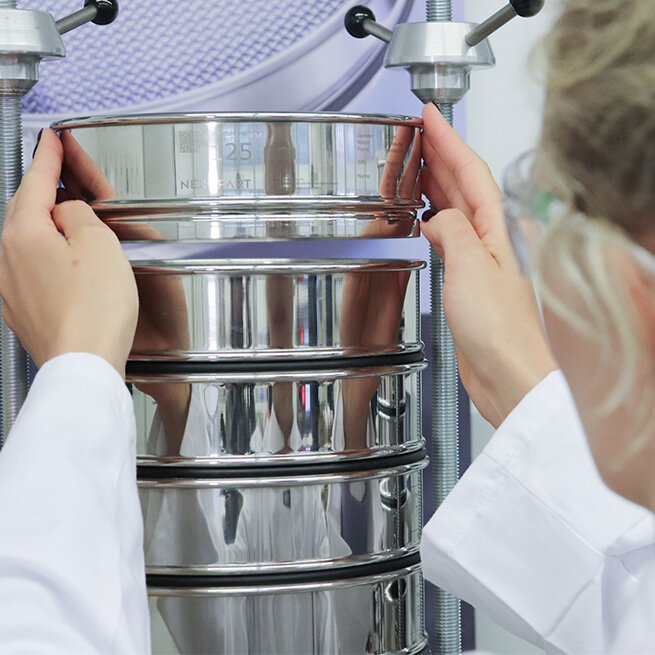
Certification and calibration. Quality assurance of sieves according to DIN standard.
With NEXOPART, you can rely on your sieving results. We use a calibrated video analysis system for the certification and calibration of new and used test sieves at our plant laboratory or with the help of a mobile unit at your site. The NEXOPART BSA measuring system meets the current version of ISO 3310-1/ DIN standard and ASTM E11 requirements for test sieves. We also carry out testing for you as recertification or recalibration.
HAVER’s calibration laboratory
We can test your sieves in the HAVER calibration laboratory of our parent company. The laboratory is accredited in accordance with DIN EN ISO /IEC 17025 DAkkS. Calibration is carried out under special measuring conditions in accordance with ISO 3310-1 for test sieves with test sieve mesh.
Please bear in mind, that testing can only be carried out in the accredited calibration laboratory of our parent company Haver & Boecker oHG in Oelde.
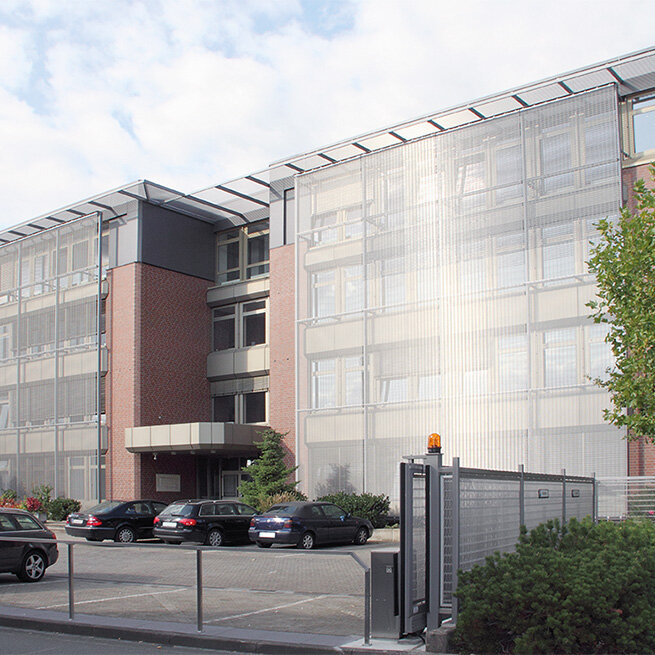
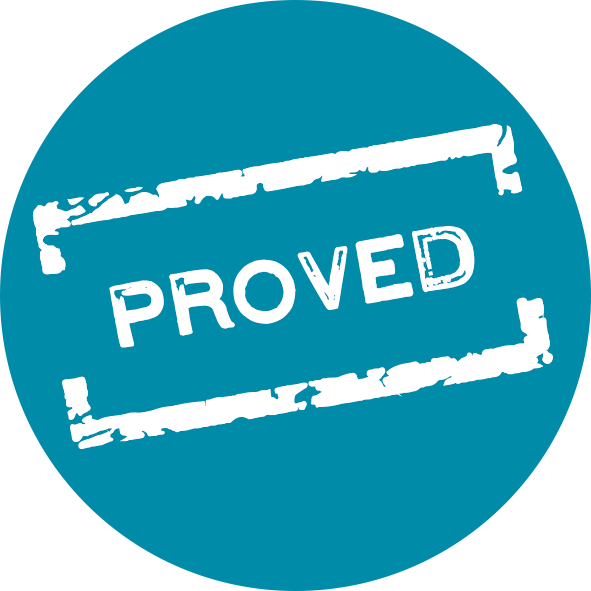
Our promise. Test sieve machines at their best.
For reliable results, you need test sieve machines that are in perfect condition. We at NEXOPART will make sure that they are. We will check the functionality, safety, and condition of each of your test sieve machines. We will also readjust or calibrate your test sieve machines - always according to your requirements of course. Following successful testing, your test sieve machines will receive a test seal and an acceptance test certificate 3.1 in accordance with DIN EN 10204.